Achieving Year on Year Improvement
Manufacturers worldwide are navigating increasingly complex challenges—rising costs, operational inefficiencies, and ever-demanding customer expectations. While many organisations strive for operational excellence, few achieve the sustained, year-on-year improvements that separate industry leaders from the rest.
Find out how our training, facilitation and coaching support can help your organisation to replicate the success of industry leading organisations.
The Path to Operational Excellence
Achieving year-on-year improvement is not just about tools or strategies—it’s about building a culture of continuous improvement.
That involves developing capabilities to join the dots between daily/weekly/monthly improvement activities so that:
The systematic reduction in hidden losses becomes part of a routine management process.
Those closest to the detail have the support and guidance where needed to identify root causes and develop effective countermeasures that prevent breakdowns, assure systematic progress toward zero defects and no touch production.
The rewards—higher efficiency, lower costs, and a more engaged workforce—are well worth the effort.
Click on the articles below to find out more then Contact us to find out more about how we work with your team to make that happen.
Why TPM Is fundamental to Excellence
Organisations that successfully deliver lasting improvement, invest time in creating TPM Centres of Excellence because it is a practical way to:
Develop workforce capability to prevent the causes of failure,
Engage front line teams with reducing the causes of accelerated wear and improving problem prevention as part of the daily routine.
Tap into the enhanced connectivity provided by digitisation and smart technology.
The outcome of this process is front line "improvement pull" which provides a vehicle for local leaders to shape outlook and reinforce proactive behaviours.
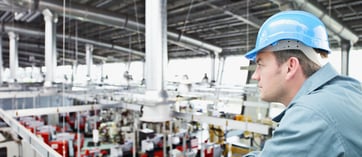
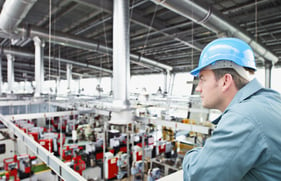
How Lean Maintenance Ratchets Up Effectiveness
Lean Maintenance supports the TPM centre of excellence programme to remove the causes of recurring problems and redirect engineer time to:
Improve asset care work routines and develop internal skills to stabilise and extend component life,
Remove waste and non value adding activities such as unplanned adjustments from work routines,
Enhance process effectiveness and release asset potential.
The outcome is increased capacity, reduced defects, improved material yield, lower energy cost per unit and improved resilience to shifts in demand.

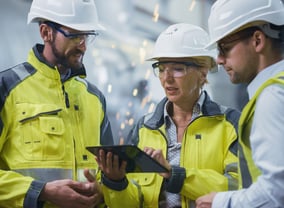
How to Deliver Better Projects Faster
Effective Project Management is an essential capability on the journey to excellence. Learn more about how to design projects to reduce risk, speed up timelines and enhance project added value. It starts with how to assess project complexity and your organisations capability to deliver flawless operation from day one.
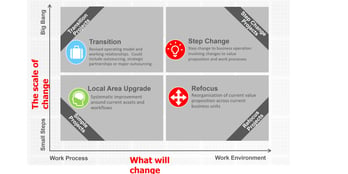
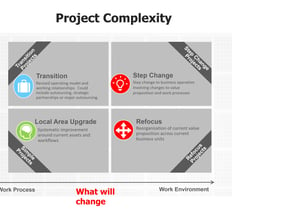
Get in Touch with Us
Let us support your performance improvement journey. Reach out today!
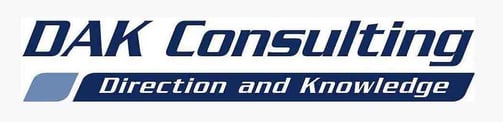

DAK Consulting
Chiltern House
45 Station Road
Henley on Thames
RG9 1AT, UK
Info@dakconsulting.co.uk
www.dakacademy.com
+44 (0)1491 845504