Achieving year-on-year improvement requires more than just tools and strategies—it involves embedding a culture of continuous improvement into daily operations. Organisations that adopt a structured approach can adapt to shifting customer expectations, technological advancements, and the pressures of rising costs and increased legislation.
The TPM Excellence Programme provides a structured framework to integrate sustainable improvements into operations. This guide outlines key steps for internal personnel to follow, with coaching support available where needed. That covers three critical areas:
Area Leadership: Empowering business leaders to capture and replicate successes, embedding them into routine management practices.
Execution: Hands-on engagement with real-world problems to develop practical solutions that improve day-to-day operations.
Planning: Systemising work routines, removing barriers to long-term improvement, leveraging data-driven decision-making, and applying smart technologies to enhance workflow and connectivity.
Embedding TPM into Local Processes
Rather than overhauling the entire organisation at once, start with a focused pilot project. This allows teams to test and refine processes before rolling out improvements more broadly.
Why Pilots Work: They deliver quick wins while uncovering deeper systemic issues.
Learning by Doing: Cross-functional teams gain hands-on experience tackling real issues, sharing knowledge, and aligning priorities.
From Quick Fixes to Sustainable Change: Identifying and removing barriers ensures improvements are long-term and repeatable.
The insights gained from pilot projects should be documented and shared across the business to embed TPM principles into daily operations.
Daily/Weekly (Execution)
Work Control: Ensure a balance between output and maintaining stable operating conditions. Implement structured problem-solving routines to improve workplace organisation and response to anomalies.
Data Management: Collect and analyse operational data to identify trends, refine standards, and drive continuous progress towards zero breakdowns.
Process Control: Local teams should set and track incremental improvement targets, using data-driven defect analysis to prevent recurring issues.
Weekly/Monthly
Policy Deployment: Review performance management insights to refine operating standards, improve compliance, and enhance asset care.
Collaboration: Build workforce capability by developing core, intermediate, and specialist skills to prevent failures and quality defects.
Performance Analysis: Regularly assess sources of wear and inefficiency, refine routine adjustments, and analyse defect causes to improve work routines and prevent unplanned downtime.
Monthly/Quarterly/Annual (Set Direction)
Quarterly Improvement Cadence: Embed systematic improvement into management routines to reinforce operational discipline.
Critical Parameter Setting: Document best practices and policy standards based on lessons learned.
Standardisation of Work Routines: Ensure work routines are formalised to support consistent improvement.
Issue Management: Capture and share lessons learned to drive problem prevention and continuous engagement.
Find out how our training, facilitation and coaching support can help you organisation to deliver those gains as part of your current or future improvement programme.
Creating TPM Excellence
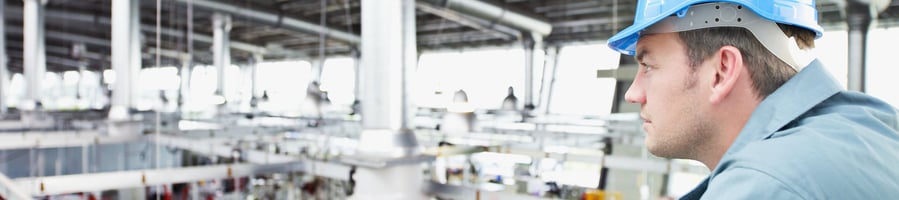
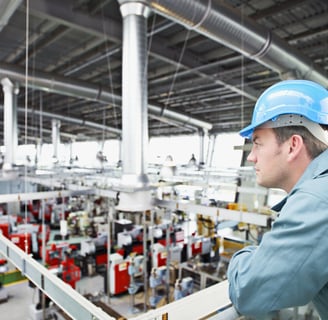
Scaling improvement efforts requires a structured approach. The Rollout Cascade process helps develop an integrated Improvement Leader Network within the organisation, ensuring alignment across teams.
Scheduling: Transition from functional to cross-functional dynamic scheduling.
Communication: Improve connectivity to enhance information flow and decision-making.
Collaboration: Align improvement priorities and ensure smooth task transfer.
Data Analysis & Decision Support: Implement structured processes for:
Error prevention
Planned interventions
Glide path to optimal operating condition.
2.0 Rolling Out Lessons Learned
The TPM Centre of Excellence programme provides a structured approach to embedding improvement at all levels of the organisation.
Recommended Next Steps for Internal Teams:
Use this guide as a reference for implementing TPM principles within your teams.
Engage cross-functional teams in pilot projects to test and refine approaches.
Establish regular review cycles to assess progress and adjust strategies as needed.
Share insights and best practices across departments to accelerate adoption.
Your organisation doesn’t have to navigate this transformation alone. Our expert consultancy, facilitation, and coaching will ensure that TPM principles are embedded seamlessly into your operations, delivering measurable results.
We can provide guidance on specific challenges, refine processes, and ensure successful implementation. Our team can assist in facilitating structured rollouts, upskilling internal leaders, and embedding best practices for long-term success.
Find out how our training, facilitation and coaching support can help you organisation to deliver those gains as part of your current or future improvement programme.
3.0 Ready to Take the Next Step?
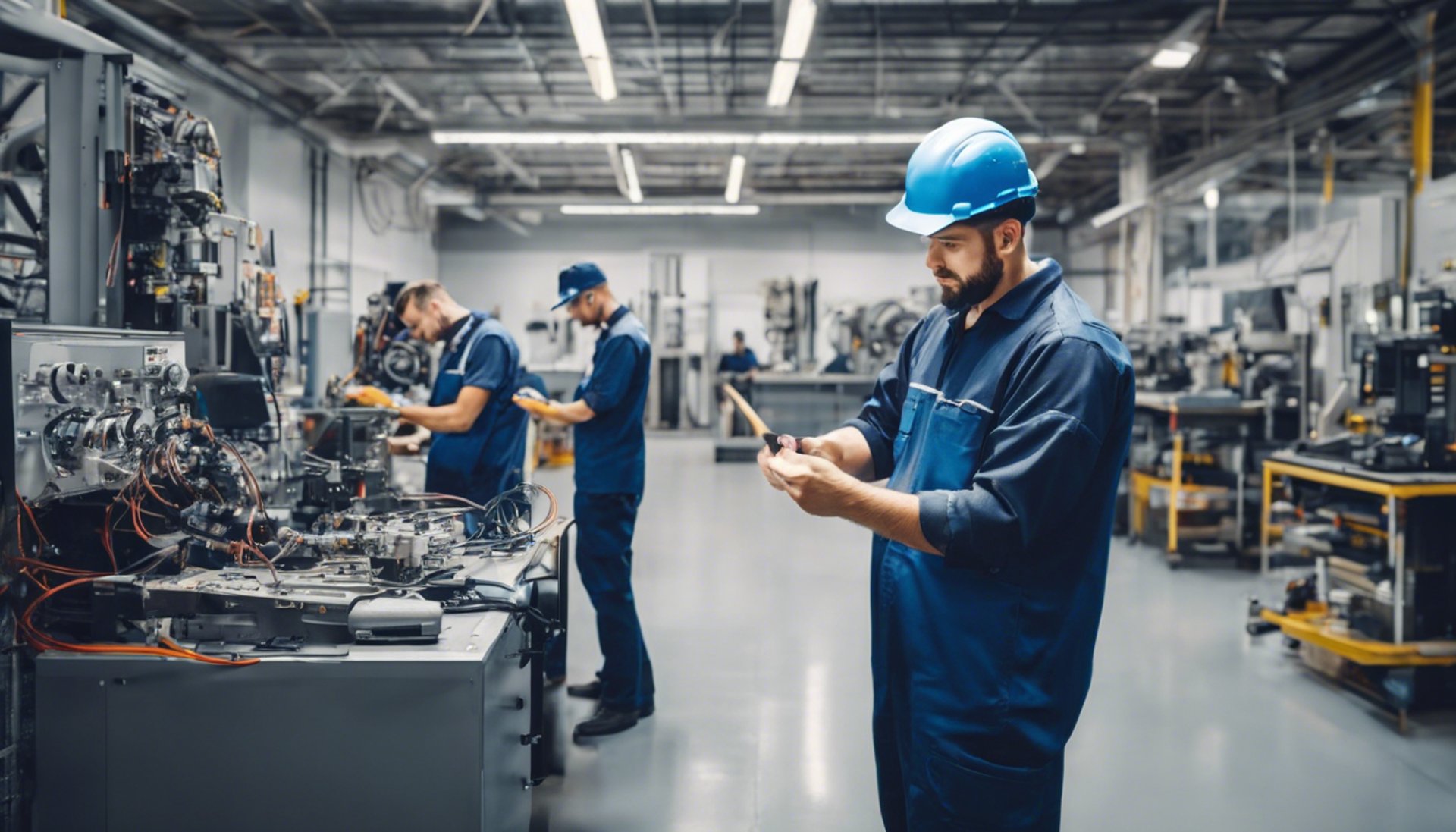
Hands On 3 Day Training Workshop
Implementing TPM Best Practice
3 Day Training Workshop
Designed specifically for those who need to know how to deliver sustained improvement in OEE and create a new shop floor reality. Includes advice on how to integrate TPM with Lean and Six Sigma programmes.
Learn how to apply Total Productive Manufacturing principles and techniques to release the full potential of your people, procedures and work processes.
Know what it takes to engage those who use and look after equipment and processes with a common goal to improve effectiveness.
Understand what it takes to secure stable and resilient operations.
Be able to achieve better than new performance from key assets.
Turn theory into practice using our structured Asset Improvement Plan workbook to apply lessons learned to production assets on the factory floor.
Assess the potential of TPM, analyse equipment criticality, set standards, develop best practice routines and raise skills to systematically increase equipment effectiveness.
With the support of the course leader, convert the lessons learned into a bespoke TPM implementation programme. One designed to win support from management and engage production and maintenance functions in a shared quest to eliminate breakdowns and improve performance.
This course provides delegates with the opportunity to understand how TPM principes are applied to live assets. That includes how to:
Apply criticality assessments to set notifications flags that support routine coordination and surface opportunities for improvement.
Target time spent on enablers such as training and asset care to enhance OEE, capacity, yield and energy gains.
Develop trouble shooting algorithms to enhance feedback, drive simplification of routine practices and remove non value added activities.
Blend the use of digitisation to automate routine with face to face interaction and visual indicators to encourage engagement, innovation and cross functional collaboration.
Course Leader: Dennis McCarthy
Get In Touch
Contact us to enhance your manufacturing processes through training, facilitation and coaching support as part of the day to day operation.
DAK Consulting
Chiltern House
45 Station Road
Henley on Thames
RG9 1AT, UK
Info@dakconsulting.co.uk
www.dakacademy.com
+44 (0)1491 845504