Ratcheting Up Improvement Gains
Through TPM Excellence
The TPM Excellence Programme is designed to enhance manufacturing performance and resilience.
The programme begins by assessing current operations and aligning leadership on improvement priorities. This is followed by a practical, hands-on phase centred around asset improvement pilots. The goal is to drive measurable results through team-led initiatives, embedding continuous improvement into daily routines and ultimately scaling successful practices across the organisation to achieve sustained excellence and meet future challenges.
The core of the support programme is a structured improvement journey that delivers immediate results while building the capabilities your organisation needs for the future. This simultaneously develops:
Leadership Competence.
Execution Excellence.
Planning and Performance Analysis.
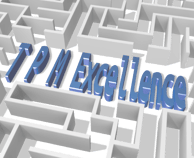
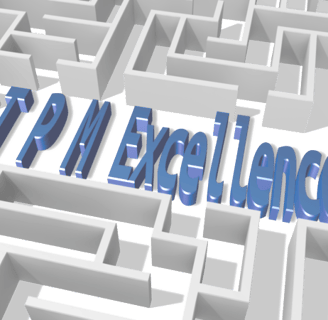
Early Equipment Management
Delivering Flawless Operation From Day One
Organisations implementing EEM have realised significant financial and operational benefits:
Up to 30% capital cost through enhanced project added value.
Up to 50% lower operational life cycle costs, enhancing long-term profitability.
In at least one case this resulted in 100% ROI within the first year for some businesses—far surpassing conventional 15% forecast returns.
Enhanced internal capabilities, leading to faster, lower-effort project execution in subsequent initiatives.
Find out more about how to apply EEM principles
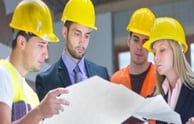
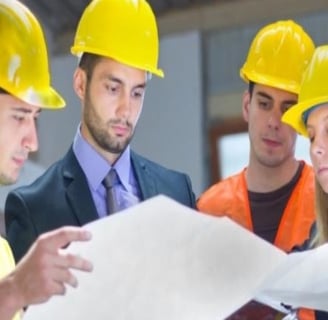
Online Excellence Health Checks
A Catalyst for Sustainable Improvement
Our diagnostic models are designed to accelerate the journey from reactive problem-solving to proactive, people-driven improvement. Based on extensive research into successful improvement roadmaps, these tools highlight both critical opportunities and common pitfalls.
Key Benefits:
Rapid, 5-minute completion per diagnostic
Confidential and zero cost
Delivers actionable insight: current status vs best practice, plus next step priorities
Focus Areas:
Click on links below and we will send you a report highlighting strengths and barriers to progress together with recommended next steps.
Outcome: A structured roadmap to deliver sustainable performance improvement.
Why It Matters: These diagnostics empower senior leaders to:
Align improvement priorities across departments
Strengthen operational and project delivery systems
Unlock the full potential of frontline and engineering teams
Leverage this proven tool to turn insight into action and accelerate business results.
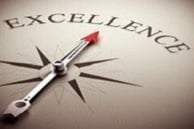

Planning The Plan
For meaningful and lasting improvements, manufacturing organisations must align priorities across all levels—from strategic leadership to frontline operations—ensuring that:
Senior management has a clear line of sight on how shop floor improvements drive long-term business success.
Frontline managers can balance daily output pressures with structured improvement activities as part of routine operations.
Frontline personnel actively contribute to performance improvements by systematically addressing unplanned events and inefficiencies.
The key to achieving this alignment are Plan the Plan sessions. Find out more
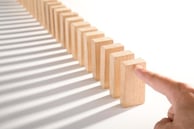
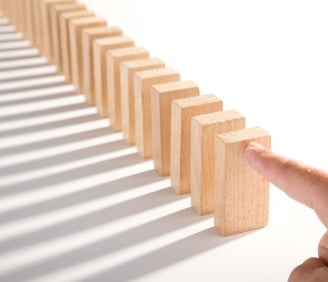
Maintaining Momentum
One of the most common reasons why improvement gains are not sustained is a lack of joined up Performance Management Processes. The missing link means that once the short term pain of immediate failures has been dealt with, the performance management radar shifts attention towards a fresh issue.
In contrast, successful organisations adopt a joined up approach to systematic improvement as part of their Performance Management Process. That means investing time to improve processes that are already working to expose and deal with deeper, systemic issues that hinder improvement.
Find out more about how we can help your organisation to develop the top down and bottom up processes to make this happen.
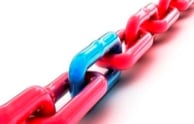
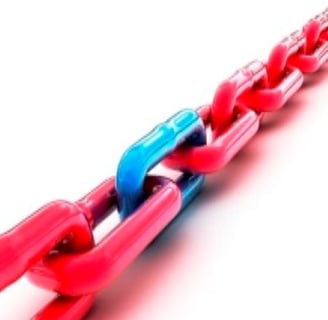
DAK Consulting
Chiltern House
45 Station Road
Henley on Thames
RG9 1AT, UK
Info@dakconsulting.co.uk
www.dakacademy.com
+44 (0)1491 845504