Plan the Plan Sessions: A Route to Meaningful Change
The key to achieving meaningful change is the use of cross functional plan the plan sessions to create an aligned 12-month leadership agenda. Here's how to do that.
3 min read

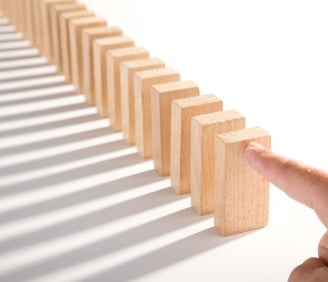
For meaningful and lasting improvements, manufacturing organisations must align priorities across all levels—from strategic leadership to frontline operations—ensuring that:
Senior management has a clear line of sight on how shop floor improvements drive long-term business success.
Frontline managers can balance daily output pressures with structured improvement activities as part of routine operations.
Frontline personnel actively contribute to performance improvements by systematically addressing unplanned events and inefficiencies.
Engaging them in resolving recurring issues for as little as 5% of their time has been shown to deliver an ROI of 15-25% per annum.
The key to achieving this alignment is the use of Plan the Plan Working Sessions as part of the performance management process.
What is a Plan the Plan Session?
A Plan the plan session brings together cross-functional team leaders and key specialists to design the forward improvement glide path to:
Confirm the need for change – Identify performance gaps and high-impact improvement opportunities.
Assess Capability to Deliver Change – Evaluate current systems, skills, and processes.
Map Out Actionable Steps – Develop a practical, results-driven improvement roadmap.
Planning the plan working sessions also build collective area leadership capabilities to meet complex business challenges like how to embrace smart technology or how to enhance performance in new markets because these sessions nurture:
Improvement Leadership.
Breakthrough thinking.
Cross-functional collaboration.
Data-driven decision-making.
Shared ownership of improvement actions.
Preparation is Crucial
Success of the working session depends on taking stock of:
Strengths & Weaknesses – Identify areas where improvements will yield the greatest impact.
Best Practices – To be able to build on existing successes rather than reinventing the wheel.
Performance Management – Establish links between Total Manufacturing Costs and performance drivers across people, processes, and procedures.
Barriers to Progress – Identify roadblocks preventing change.
Business Drivers & Priorities – Align improvement initiatives with strategic objectives.
This provides a readiness assessment ensures that Plan the Plan sessions focus on the most critical improvement areas and provide a clear agenda.
Setting the Plan the Plan Agenda
The TPM Excellence programme uses the readiness review outputs to identify gaps, barriers and opportunities for improvement. This sets the agenda for the next Plan the Plan working session to raise awareness of current status and set the scene to help delegates to develop forward action plans covering:
Daily Management
Where are we now and what do we need improve?
What is the current level of operational capability?
Policy Deployment
What hidden losses should be targeted?
What will the improvement glide path look like?
Process Control and Asset Reliability
Where are the high-risk failure points?
What corrective actions are needed?
Cross Functional Improvement Roles
How will compliance be assured?
How will feedback be used to make tasks easier to execute correctly?
Standardisation
How effective are current work routines?
What areas need attention?
Performance Analysis
How will future progress be measured?
What are the next steps for scaling improvements?
Delivering Tangible Business Impact
The structured approach of Plan the Plan sessions enables organisations to craft an improvement roadmap that drives operational excellence through:
🔹 Robust frontline work practices – Reducing waste, improving workflow, and eliminating non-value-added activities.
🔹 Proactive maintenance transformation – Shifting from reactive repairs to a resilient, reliability-centred approach.
🔹 Enhanced project specifications & execution – Driving higher value from improvement initiatives, ensuring flawless day-one operations.
The Power of Pilot Projects
For organisations new to Plan the Plan sessions, starting with a focused pilot project in a high-priority area can accelerate engagement and demonstrate impact.
Why Pilots Work:
Quick Wins & Deep Insights – They deliver rapid improvements while exposing underlying systemic issues.
Learning by Doing – Hands-on problem-solving helps teams align priorities and develop lasting solutions.
From Fixes to Sustainability – Beyond short-term solutions, pilot projects identify and remove the root causes of recurring issues.
Scaling Success
To embed improvements across the organisation, the lessons from pilot projects are deployed through a structured roll-out cascade covering:
Strategic Leadership Alignment – Ensuring that improvement priorities drive business development.
Execution Excellence – Equipping cross-functional teams with the skills and systems to integrate improvements into daily routines.
Sustainable Improvement Roadmaps – Establishing structured processes to remove barriers, systemise work routines, and leverage data & smart technology for enhanced operational performance.
Why Plan the Plan Sessions are a Game-Changer for Manufacturing Leaders
Routine working sessions with team leaders and key stakeholders as part of the quarterly improvement cycle provides a practical forum to feedback progress, raise awareness of improvement priorities and build area leadership capabilities to:
Align shop floor activities with long-term business goals.
Drive improvement ownership & accountability across the business.
Unlock new thinking to secure measurable performance gains
Ensure sustainable, scalable improvements.
This is not just about short-term problem-solving—it’s about embedding a culture of continuous improvement that drives long-term competitive advantage.
Would you like to discuss how we can tailor Plan the Plan working sessions for your organisation? Let’s connect.
DAK Consulting
Chiltern House
45 Station Road
Henley on Thames
RG9 1AT, UK
Info@dakconsulting.co.uk
www.dakacademy.com
+44 (0)1491 845504