Accelerate Improvement with Targeted Diagnostics
The path to sustained success in today’s fast-changing manufacturing landscape is complex. Customer expectations, workforce dynamics, advancing technologies, and tightening legislation constantly shift the goalposts. These shifts often expose hidden gaps in management systems, gaps that hinder progress and erode performance. You might already be seeing the signs:
Frequent plan changes.
High levels of short stops.
Unexpected component failures.
Our research into the improvement roadmaps of high-performing organisations confirms a fundamental truth: sustained success hinges on moving from reactive management to proactive, people-driven improvement. Once practices that eliminate breakdowns are in place, the focus shifts—from firefighting to preventing the root causes of minor defects. This transformation in leadership and engineering behaviour unlocks significant performance gains. We’ve developed a set of rapid self-assessment diagnostics to help you stay on course. Grounded in proven best practice, these tools:
Pinpoint your current position on the improvement journey
Identify critical barriers and priority opportunities
Provide a practical, prioritised roadmap to deliver results
CI Maturity Health Checks
Assess your operational excellence status across Customer Service, Operations, and Technology functions. Learn how to align your teams and accelerate next steps.
Operational Performance Management
Review how performance analysis and data use align with your current stage of improvement. Identify where refinements can unlock further progress.
Evaluate the maturity of your maintenance strategy. Identify how to ratchet up reliability and effectiveness through proactive practices.
Understand your organisation’s capability to transfer lessons learned from improvement gains into new assets. Understand where to apply Early Equipment Management principles.
Click on the above links to complete your assessment:
Takes just 5 minutes per diagnostic
No prep required, 100% confidential
Produces a free benchmark report with:
Your current performance vs best practice.
Recommended priorities and next steps.
The diagnostic results can be used to align leadership, energise teams, and focus your improvement effort where it matters most.
How We Can Help
The diagnostic content is based on research into successful improvement journeys which identified four management systems that directly impact on performance, these are:
Process Control: This governs asset-level tasks, including preventive maintenance, inspection standards, servicing schedules, and best-practice routines. Effective process control reduces variability and ensures consistent output.
Leader Standard Work: This defines routine tasks for normal operation and asset care and priorities for improvements to future performance. Enhancing this system is central to progress from reactive to proactive maintenance.
Use of Data: That includes access to performance data, work instructions and use of feedback to update standards. The way data is used and provision of visual indicators impacts on outlook, level of engagement and problem ownership.
Planning: Coordinates resource allocation, anticipates resource needs, and captures lessons learned to continuously refine and enhance performance. Planning holds the key to locking in the gains and progress along the improvement glide path.
Underpinning the above are systems that drive cultural outlook and buy to change, These are:
Policy Deployment: To translate business priorities into clear, actionable improvement goals. This ensures alignment between corporate objectives and frontline execution.
Collaboration: To shape collective workforce capabilities, accountabilities and skill development. This also impacts on the quality of feedback and sharing of lessons learned.
Performance Analysis: To deliver data-driven insights to identify causal factors, track progress, and drive continuous improvement initiatives.
Where to Start
Your diagnostic results will highlight where to dig deeper to identify:
What’s working well—and where the greatest improvements lie
Root causes driving unnecessary costs and complexity
Alignment gaps between business goals and shop floor performance
A tailored capability roadmap for your strategic priorities
We work with you to:
Raise awareness of improvement gaps with area leaders
Build local ownership and commitment to change
Map out quarterly action cycles to drive sustainable results
Embed improvement priorities into business planning rhythms
Whether your focus is leadership, execution, or planning, we support you in fixing systemic gaps, capturing lessons, and locking in performance gains.
That includes mapping out next steps using quarterly action cycles to set the heart beat for delivering long-term improvement priorities across the site. These cycles are linked to annual business planning goals to ensure traction, continuity, and measurable outcomes.
Depending on where you are on the journey this might involve fixing gaps in shop floor systems and accountabilities such as:
Leadership: Capturing lessons learned as standards and developing capabilities to comply with those best practice standards
Execution: Providing quality feedback on issues and opportunities for improvement to systemise routine tasks and share lessons learned.
Planning: Enhancing planning feedback loops to lock in gains and ratchet up performance.
Once these accountabilities are in place and working, the enhanced work routines provide the foundations for a continuous cycle of improvement that enhances organisational performance.
You are not on your own. Contact us to find out more about how we can help you to apply these insight to remove barriers and accelerate progress.
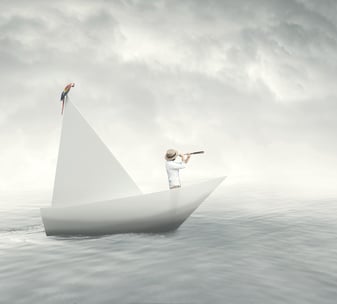
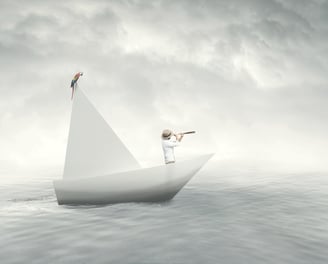
DAK Consulting
Chiltern House
45 Station Road
Henley on Thames
RG9 1AT, UK
Info@dakconsulting.co.uk
www.dakacademy.com
+44 (0)1491 845504