Assessing Maintenance Readiness
Click on the button below to complete our on line Maintenance Management Diagnostic and we will send you a short report on how to remove barriers to improvement and place Maintenance at the heart of Operational Excellence.
The diagnostic covers the following maintenance systems.
Lean Asset Management
Process control
How effectively do you identify and resolve operational challenges to ensure each asset is delivering its full potential?Policy Deployment
How proactive and effective is your approach in addressing the root causes of failures and reducing problem hot spots?
Lean Execution
Work Control
How well-defined are the roles and responsibilities for initiating corrective actions and preventing future incidents?Skill Development
How structured and comprehensive is your program for developing technical skills and enhancing teamwork within the operations team?
Lean Improvement
Planning
How effective is the standardisation of your key maintenance processes, including asset inspections, servicing, technical data management, work planning, daily operations, cost control, and the management of spares and lubrication?Performance Analysis
How clearly defined is your long-term vision, and how well do your 12-month and 90-day action plans align to support that vision?
Mobilising Lean Maintenance
The output from the diagnostic provides maintenance management with an agenda for a plan the plan session to map out targeted action plans to deal with priority gaps in Leadership, Execution, and Improvement processes. The deliverables from this first phase is a programme to establish basic asset conditions, upgrade documentation, knowledge, workflow and spares management to establish:
Lean Asset Management covering preventive maintenance, inspection and servicing routines,
Lean Execution covering standardisation, systemised workflows and engagement,
Lean Improvement covering skill development, performance management, focussed improvement and engagement.
Find out how our training, facilitation and coaching support can help you organisation to deliver those gains as part of your current or future improvement programme.
Implementing Lean Maintenance
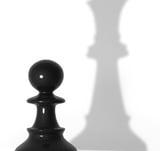
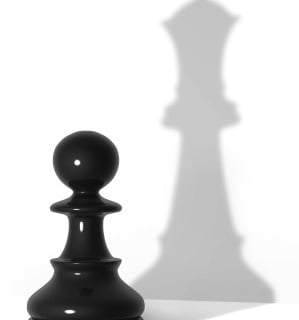
Lean Maintenance applies Systems Thinking to maintenance practices, shifting the focus from isolated tasks to a comprehensive, end-to-end approach.
Instead of managing tasks independently, systems thinking ensures that maintenance activities are interconnected, defining clear triggers for action and structured responses. The outcome is to move beyond simply preventing downtime to proactively optimising process effectiveness and eliminating waste.
This shift has significant benefits including:
Extended Component Life – Studies show that a systems-based approach can stabilise and extend component lifespan by up to 50%.
Improved Efficiency – By optimising maintenance as part of the larger system, material yield, capacity, and energy efficiency see measurable improvements.
Enhanced Maintenance Value – Rather than reacting to breakdowns, maintenance becomes a proactive force that enhances overall equipment performance.
Lean Maintenance also complements the TPM centre of excellence program by redirecting the time saved from reducing breakdowns towards activities to optimise asset performance. In addition to improving capacity and resilience, this also
Reduces unplanned interventions such as minor stops to improve operator productivity,
Stabilises and extends component life,
Improves process precision, quality yield, energy efficiency,
Reduces manufacturing costs.
Apply Lean Maintenance principles by building on existing good practices. A good place to start is with an assessment of Maintenance Readiness.

Lean Maintenance
Implementing Lean Maintenance
3 Day Accelerator Training Workshop
Pick up to 3 troublesome assets and during this 3 day accelerator workshop, delegates will apply the Lean Maintenance workbook to them to systematically assess the current shop floor reality against best practice benchmarks. This includes practical team based, shop floor activities to apply:
Lean Asset Management covering preventive maintenance, inspection and servicing routines,
Lean Execution covering standardisation, systemised workflows and engagement,
Lean Improvement covering performance management and use of data.
In addition to improving asset reliability participants will identify how to refocus the time released to enhance process effectiveness, resilience and flexibility. That includes adapting work routines to take advantage of advances in technology and digitisation.
The training workshop content leads delegates through the theory and practices of how Lean theory applies to Maintenance routines. The lessons from the practical activities are used to illustrate how following the Lean Maintenance road map can deliver:
Effective Maintenance Execution by highlighting non value adding Maintenance routines and opportunities to enhance production and maintenance asset care workflows,
Robust Process Stability by targeting problem hot spots, early problem detection and problem prevention routines,
Enhanced Process Resilience by dealing with sources of accelerated wear including contamination and human error,
Improved Flexibility of resources using standards and visual management to systemise routine tasks to make it easier to achieve core competencies,
Reduced Manufacturing Costs by systematically resolving the causes of reactive maintenance to stabilise and extend component life.
The final session of the workshop involves the development of a bespoke Lean Maintenance route map to release maintenance resource to improve asset effectiveness. A transition from the traditional maintenance outlook of preventing downtime to one of preventing defects to deliver the full value adding potential of the maintenance function.
In addition to the above benefits, incorporating Lean Maintenance within a Lean, TPM or Six Sigma programme has been shown to increase annualised gains by as much as 50%.
Course Leader: Dennis McCarthy
Get In Touch
Contact us to enhance your manufacturing processes through training.
DAK Consulting
Chiltern House
45 Station Road
Henley on Thames
RG9 1AT, UK
Info@dakconsulting.co.uk
www.dakacademy.com
+44 (0)1491 845504