Transforming Maintenance to Release Engineer Added Value
Lean Maintenance transforms the maintenance role from fixing breakdowns to releasing the full potential of operational equipment and processes by delivering: Lean Asset Care covering preventive maintenance, inspection and servicing routines, Lean Execution covering standardisation, systemised workflows and engagement, Lean Systems covering stores, performance management and CMMS.
3 min read
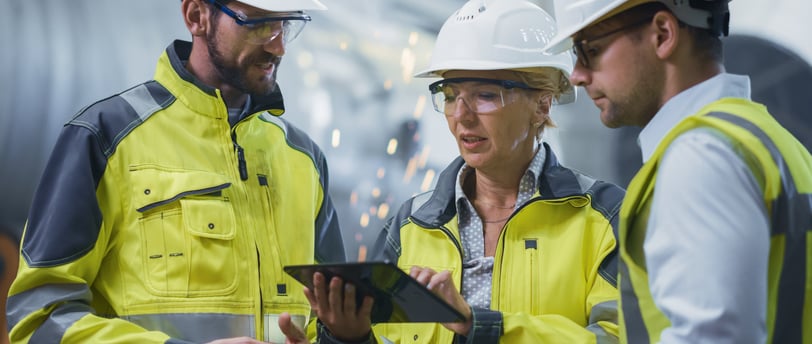
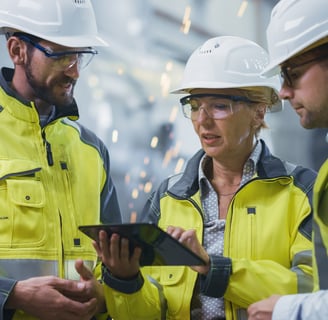
Understanding Lean Maintenance
In the fast-paced world of operational management, lean maintenance emerges as a vital strategy. Traditionally, the maintenance role has been perceived strictly as a reactive function, primarily focused on resolving equipment breakdowns. However, the lean maintenance framework pivots this viewpoint by emphasizing the potential of operational equipment and processes. Through a systematic approach, it ensures that maintenance transforms from a mere fixing operation into a strategic contributor that unlocks significant value within organizations.
The Lean Maintenance Process
Lean maintenance revolves around several core components designed to enhance operational effectiveness. First, lean asset care integrates preventive maintenance, inspection, and servicing routines, shifting away from reactive methods towards proactive measures. This approach not only prevents breakdowns but also maximizes equipment longevity and performance.
Next, lean execution works on standardisation and systemised workflows. It accelerates the maintenance processes by eliminating redundancies and engaging team members effectively. By implementing a structured framework, organizations can ensure that every action contributes towards achieving operational goals, thus boosting overall productivity.
Finally, the importance of lean systems cannot be overstated. This aspect encompasses comprehensive management systems like CMMS (Computerized Maintenance Management Systems), which improve inventory control and performance management. By systematically addressing these areas, lean maintenance equips organisations to optimise their supply chains, minimize waste, and significantly reduce non-value-adding activities.
The Gains from Lean Maintenance
Adopting a lean maintenance approach allows businesses to realise substantial gains. Not only does it free up time traditionally spent on firefighting breakdowns, but it also releases valuable resources that can be dedicated to enhancing process effectiveness, resilience, and flexibility within operations. With more time available, teams can focus on impactful activities that drive long-term value.
The process of adopting a lean maintenance methodology supports organisations in adapting their work routines in alignment with technological advancements and digitisation trends. Embracing new technologies not only enhances the efficiency of maintenance tasks but also provides real-time data insights, leading to smarter decision-making and improved operational capabilities.
In conclusion, lean maintenance redefines the role of maintenance within organisations, guiding it towards a future where maintenance improvement forms the backbone of operational excellence. The transformation involves not only a shift in mindset but also a commitment to systematically reducing waste, thereby unleashing the full potential of existing processes and equipment.
Pick up to 3 troublesome assets and during this 3 day accelerator workshop, delegates will apply the Lean Maintenance workbook to them to systematically assess the current shop floor reality against best practice benchmarks. This includes practical team based, shop floor activities to apply:
Lean Asset Care covering preventive maintenance, inspection and servicing routines,
Lean Execution covering standardisation, systemised workflows and engagement,
Lean Systems covering stores, performance management and CMMS.
In addition to improving asset reliability they will identify how to refocus the time released to enhance process effectiveness, resilience and flexibility. That includes adapting work routines to take advantage of advances in technology and digitisation.
The training workshop content leads delegates through the theory and practices of how Lean theory applies to Maintenance routines. The lessons from the practical activities are used to illustrate how following the Lean Maintenance road map can deliver:
Effective Maintenance Execution by highlighting non value adding Maintenance routines and opportunities to enhance production and maintenance asset care workflows,
Robust Process Stability by targeting problem hot spots, early problem detection and problem prevention routines,
Enhanced Process Resilience by dealing with sources of accelerated wear including contamination and human error,
Improved Flexibility of resources using standards and visual management to systemise routine tasks to make it easier to achieve core competencies,
Reduced Manufacturing Costs by systematically resolving the causes of reactive maintenance to stabilise and extend component life.
The final session of the workshop involves the development of a bespoke Lean Maintenance route map to release maintenance resource to improve asset effectiveness. A transition from the traditional maintenance outlook of preventing downtime to one of preventing defects to deliver the full value adding potential of the maintenance function.
In addition to the above benefits, incorporating Lean Maintenance within a Lean, TPM or Six Sigma programme has been shown to increase annualised gains by as much as 50%Write your text here...
Implementing Lean Maintenance
3 Day In House Training Workshop
DAK Consulting
Chiltern House
45 Station Road
Henley on Thames
RG9 1AT, UK
Info@dakconsulting.co.uk
www.dakacademy.com
+44 (0)1491 845504