Where Project Training Drives Up Project Results
Effective project delivery is critical to long term business results. Those that do this well have learned how to develop internal capabilities across three project workflows. Here is how to do that.
Dennis McCarthy
3 min read
Projects are an important part of the journey to industry leading performance. That can range from the introduction of simple devices to creation of new facilities. That means that effective project management is critical to delivering long term business results.
Research shows that only around 50% of the issues that impact on that success are covered by the traditional project manager role. Early Equipment Management was developed in response to the challenge of dealing with the remaining 50% which are the main contributors to project failure. challenges, by leading manufacturers determined to do better.
That involved defining the accountabilities of other project stakeholders and developing their collective capabilities to deliver the following three project workflows.
1. Design and Performance Management
This workflow involves the creation of design goals based on the knowledge and experience of:
Process Technology to establish safety and reliability expectations.
Operations teams to set benchmarks for operability and maintainability.
Customer Facing stakeholders to define customer value and life cycle cost drivers.
By structuring these design goals against a formal 1-to-5 scale (where 3 is Acceptable and 5 is Optimum), cross functional project teams can systematically highlight critical standards and identify project risk areas. Low scores flag a higher likelihood of human error, accelerated wear, short stops and quality defects. Things that are difficult to measure but account for more than 80% of asset performance losses.
To achieve this, project stakeholders must be equipped to:
Define the project scope and detailed specifications.
Make objective decisions on vendor selection, manufacturing processes, installation, and commissioning.
Track project progress to transition smoothly from concept to project delivery to full operational capability.
Training in this area ensures that project teams can consistently deliver value by adhering to a structured approach that builds on experience of the current shop floor reality. It also helps with the development of insights into how new assets and technology can deliver operational gains.
2. Project and Risk Management
Projects involve hundreds of interdependent decisions. When roles, accountabilities, and priorities are unclear, the probability of costly delays increases sharply. Project and risk management processes require both administrative precision and leadership skills. It involves:
Facilitating milestone planning to align priorities and coordinate stakeholder activities.
Utilising stage-gate reviews to ensure projects stay on track, trap latent project defects early and foster cross-functional engagement.
Utilising adaptive project management techniques like piloting and rapid scaling when necessary.
A key element of best practice is the use of witnessed inspections to assure delivery against project goals at every stage, from concept to beneficial operation. That confirms progress but also surfaces latent project weaknesses early when they are cheaper to resolve.
When project teams are trained in these methods, they can forge stronger, win-win relationships with vendors and navigate risks more effectively, resulting in a smoother project lifecycle. Collaborative problem-solving when issues arise further strengthens these relationships.
3. Specification and Life Cycle Cost Management
This workflow manages the evolution of the project documents from tender to operational readiness including:
Concept layout design goal definition and visualisation.
Invitation to Tender specification, vendor selection and detailed planning
Factory Readiness plans including the creation of a new working culture prior to day one operation.
Tactics for ramp up and achievement of self sustaining operations.
From initial project definition to full operation, these documents firstly record key decisions as working assumptions with details added at each project milestone to formalise:
Area Leadership: Local management processes, data management and trouble shooting
Execution: SOP and Capability development for Normal Operation, Set up and problem prevention
Planning: Layouts, Material flow, Production, Inspection, Servicing,
During these steps, decision making is supported by the use of Life Cycle Costing (LCC) to enhance project value and minimise the total cost of ownership. That might include low cost or even no cost fixes to existing problem hot spots. While LCC is sometimes seen as complex, this is mostly used to compare options which can normally be carried out using a simple rapidly developed model. In addition to increased project added value, this processes increases internal project ownership, operational performance and readiness for "day-one" success.
Training in this area focuses on:
Evolving design goals into a comprehensive operational blueprint.
Developing internal ownership of methods that prevent downtime and quality defects.
How to create work routines that are easy to do right and simple to learn.
This ensures that the project doesn’t just meet its initial goals but provides a platform to deliver the full potential of the new operation, minimising total manufacturing costs and enhancing operational effectiveness.
Capturing and Applying Lessons Learned
A frequently overlooked aspect of project management is the opportunity for learning and improvement. Projects provide valuable insights, and when project teams are trained to capture lessons learned, these can be applied to future projects. This leads to continuous improvement, helping teams deliver better projects faster.
Conclusion
For manufacturing organisations, investing in project team training is not just a smart decision—it is essential for long-term success. By empowering teams with best practices in design, performance management, risk management, and life cycle cost management, organisations can streamline project delivery, reduce risks, and achieve flawless operations from day one.
Learn about our 3-day Manufacturing Project Management course, designed to provide project stakeholders with the tools, techniques, and insights needed to successfully manage complex projects from concept to completion. The course covers all essential aspects of project management, emphasizing collaboration, risk management, and steps to deliver flawless operation from day one.
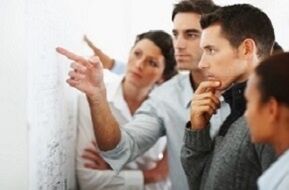
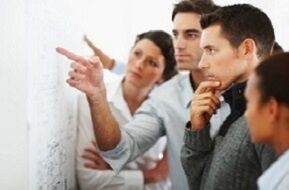
DAK Consulting
Chiltern House
45 Station Road
Henley on Thames
RG9 1AT, UK
Info@dakconsulting.co.uk
www.dakacademy.com
+44 (0)1491 845504