Using Data to Unlock Excellence
To unlock the value of data organisations need to develop the collective capability to use data to gain insights into causal factors, act on that information and drive a proactive, continuous improvement culture. Find out how to make that happen.
2 min read
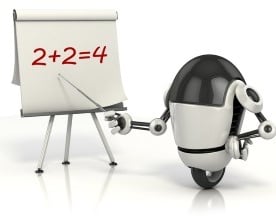
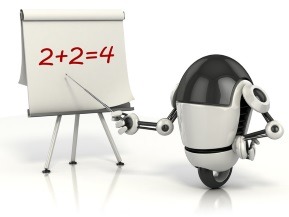
Data Capture — Basic data collection to meet financial reporting needs.
Data Sharing — Performance data captured and shared, but not yet acted upon by those collecting it.
Prioritise — Data used to set improvement priorities and targets.
Analyse — Data leveraged to improve repairs, design, spare parts storage, tools, troubleshooting and problem detection.
Optimise — Data fully integrated to optimise processes and deliver step-out product and service performance.
Progression through these steps leads to the creation of systems and processes build on rule based decision models such as:
Early warning systems — making Normal Conditions visible and defining prompt action when deviations occur.
Troubleshooting algorithms — formalising root cause analysis and response methods at common trouble hotspots.
Work standards — embedding compliance to best practices and ensuring a continuous feedback loop to refine methods.
That underpins the systemisation of routine tasks, release of specialist time and the delivery of significant year on year improvement in performance.
Making it Happen
The attention to detail needed to develop such decision models can only be achieved by engaging front line personnel in their design and development.
Each step of the TPM Excellence Roadmap develops front line capabilities to use data to deliver measurable gains. For example
Milestone 1 Detect and resolve abnormal conditions
Data used to highlight critical asset conditions
Measurable gains include reduced lost time and lower spares costs.
Milestone 2 Simplify complex routines
Data used to define "Normal Condition" standards and highlight deviations.
Measurable gains include reductions in human error and greater problem ownership
Milestone 3 Improve compliance to best practice
Data used to refine and transfer core routines to front line teams.
Measurable gains include enhanced process control and yield improvement.
Milestone 4 Identify and remove minor defect causes
Data used to reduce unplanned and then planned interventions; support low-cost automation.
Measurable gains include productivity gains and improved material yield.
The improvement project work is executed as part of daily operations and supports:
The delivery of business plans and strategic goals,
Rule based decision making and task transfer,
Measurable progress towards world-class operational performance,
Development of self correcting team capabilities.
Where an organisations is embracing advanced technology or digitisation, TPM Excellence provides a roadmap to unlock stranded data from PLCs or make use of smart sensor technologies by providing answers to questions about:
What data to capture,
How to capture it,
How to engage and empower the workforce with new insights,
How to transfer lessons learned across the business to maximise impact.
The Competitive Advantage
The TPM Excellence programme provides your teams with the skills to deliver faster, better results through smarter use of data.
That enhances operational performance, accelerates the delivery of gains and builds genuine ownership of business problems where they happen. Puttling responsibility for the solution closest to the problem.
Contact us to discuss how we can help unlock these capabilities across your organisation to accelerate your path to industry-leading performance.
Traditionally, data collection has been focused on reporting what happened and when things went wrong, to explain why, or worse, to allocate blame.
The true value of data is unlocked when the data is transformed into actionable insights through:
Understanding the causal factors behind the numbers and the decisions they inform.
Empowering people to act on that information quickly.
Using real-time feedback to refine responses.
Sharing lessons learned to multiply gains and drive a proactive, continuous improvement culture.
The development of capability to do changes the purpose of data usage through the steps of:
DAK Consulting
Chiltern House
45 Station Road
Henley on Thames
RG9 1AT, UK
Info@dakconsulting.co.uk
www.dakacademy.com
+44 (0)1491 845504