Locking in Lessons Learned
While many organisations strive for operational excellence, few manage to progress past problem solving to lock in lessons learned. This article covers how to do that and achieve the sustained, year-on-year improvements that distinguish industry leaders.
5/7/20253 min read
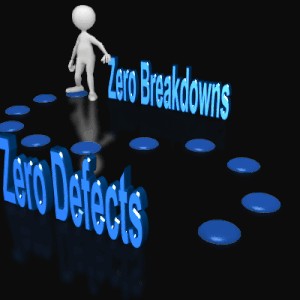
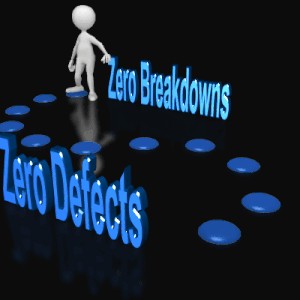
What is Policy Deployment?
Policy deployment is the process that converts best practice into standards to first achieve stable conditions then target business led performance priorities across functional areas. It locks in the foundations to reduce variability, address deeper causes of defects and release operational potential.
The TPM Excellence programme incorporates policy deployment by translating lessons learned from improvement efforts into robust policy standards for current and future assets. This ensures successful solutions are not only sustained but can also easily scaled across the organisation.
Evolving Policy Deployment in Practice
Five maturity benchmarks can be used to guide the development of policy deployment standards during the improvement journey. These benchmarks reflect an organisation’s growing ability to systematise learning, deploy standards, and link day-to-day improvements with strategic outcomes:
Set Normal Condition Standards
Action: Define operating standards and clarify what “good” looks like.
Benchmark: Standards in place for troublesome assets and trending data used for decision-making.
Resolve Problem Hot Spots
Action: Identify and eliminate root causes of issues such as trips, jams, or rework.
Benchmark: Visual control of normal vs abnormal conditions and consistent containment actions.
Improve Resilience
Action: Strengthen equipment and processes to reduce stress and failure risks.
Benchmark: Demonstrable progress towards zero unplanned breakdowns.
Manage Minor Defect Phenomena
Action: Diagnose and address early-stage defect signals through structured countermeasures.
Benchmark: Shift from reactive downtime control to proactive defect elimination.
Raise Quality Standards
Action: Categorise and address defects, with a focus on high-priority failure modes.
Benchmark: Annual improvements in yield, reliability, and resilience.
These stages are not abstract—they are achieved through practical, cross-functional projects that build frontline capability and drive top-down leadership of the improvement process.
Making it Happen: Combining Leadership and Practical Delivery
Before any improvement journey, the programme begins with a clear diagnosis:
Strengths and Weaknesses – Understand what’s working and where change is needed.
Good Practices – Leverage existing systems and build incrementally.
Common Pitfalls – Avoid superficial fixes by tackling systemic barriers.
The TPM Excellence methodology then supports organisations through five integrated stages:
Strategic Alignment through ‘Plan the Plan’ Sessions
Functional leaders, guided by consultants, prioritise improvement opportunities aligned with business goals. The result is a practical roadmap rooted in existing good practices. This builds senior-level alignment and prepares for meaningful execution.Mobilisation and Capability Development
Hands-on workshops introduce TPM tools and principles. Cross-functional teams work on real business issues, identifying quick wins and piloting low-cost countermeasures. This phase builds grassroots ownership and confidence in the process.Practical Implementation with On-the-Job Support
Frontline teams apply and refine improvements in live environments, supported by weekly coaching. This structured learning cycle promotes skill development, fosters a coaching culture, and drives operational ownership from the bottom up.Institutionalising Improvement via Performance Management
Improvements are integrated into business-as-usual via governance processes. Key metrics are tracked, progress is monitored, and—critically—successful practices are codified into policy standards, ensuring repeatability and scalability across the organisation.Leveraging Lessons for Long-Term Capability
Each improvement cycle feeds into the next through:A culture of recognition and continuous learning
Defined technical standards (e.g. for Equipment & Engineering Management)
Better capital planning and reduced lifecycle costs
This structured capture and reuse of lessons learned drives a continuous loop of improvement—ensuring what works in one area becomes standard practice everywhere.
Deliverables
The TPM Excellence programme transforms improvement from a one-off event into a habitual part of business life. Through a combination of structured diagnostics, practical implementation, and leadership engagement, organisations:
Build both technical capability and change confidence
Foster a culture that rewards learning and standardisation
Develop scalable standards based on real results from real projects
This dual emphasis on bottom-up delivery and top-down leadership ensures that improvements are not only effective but enduring.
Contact us here to find out how we can help you apply the TPM Excellence programme to embed policy deployment into your operations, accelerate capability growth, and achieve industry-leading performance.
While many organisations strive for operational excellence, few achieve the sustained, year-on-year improvements that distinguish industry leaders.
In reactive environments, human error contributes to over 50% of recurring problems. Knowledge and skill gaps account for another 35%, both of which stem from weaknesses in the Policy Deployment process. These weaknesses often reflect a lack of accountability in three key areas:
Reliable completion of routine tasks such as asset care.
Formalised standard setting to reduce the need for technical judgement.
Training to ensure consistent execution.
Without these foundations, problems persist unnecessarily, consuming time and resources. Even when solutions are found, they are rarely shared or scaled.
DAK Consulting
Chiltern House
45 Station Road
Henley on Thames
RG9 1AT, UK
Info@dakconsulting.co.uk
www.dakacademy.com
+44 (0)1491 845504