Lean Systems That Enhance Maintenance Value
Lean Maintenance applies systems thinking to maintenance processes. Not to be confused with IT systems, these are systems of work that directly impact on customer value and enhance overall efficiency.
3 min read
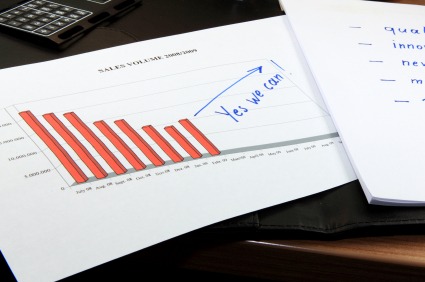
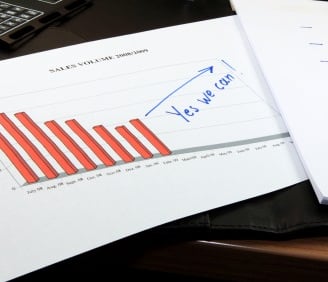
The principles of Lean Manufacturing have demonstrated that optimising entire processes delivers far superior results than simply improving individual tasks. This holistic, end-to-end approach—also known as systems thinking has the potential to enhance how Maintenance performance too.
Lean Maintenance applies systems thinking to maintenance processes to directly impact on customer value and enhance overall efficiency. It also provides a vehicle to deliver a proactive improvement culture and place Maintenance at the centre of Operational Excellence.
Not to be confused with IT systems such as CMMS, Lean Maintenance adopts a systems approach to group together tasks based on their impact on added value. For example, Lean Maintenance addresses Planned Maintenance (PM) as part of the Process Control System rather than as individual inspection and servicing tasks. The change of emphasis is then used to assess PM added value and provide a trigger for innovation to foster a continuous improvement outlook. It also positions maintenance at the heart of operational excellence where it belongs. Routine actions such as daily asset care and prevention checks are addressed as part of Leader Standard Work systems, Task design, workflow, spares management and trouble shooting are addressed as part of Planning systems.
Implementing Lean Maintenance
Implementing Lean Maintenance involves actions to deal with the causes of reactive maintenance so that time can be diverted to more value adding activities. Ideally, this builds on existing good practices which means that the content of the implementation road map depends on the current level of maintenance maturity. Below are examples of typical improvement areas under each Lean Maintenance System. (For a better understanding of how current practices can be enhanced through Lean Maintenance, complete our free online self assessment diagnostic and we will send you a report.)
Improving Process Control
Identify and Address Sources of Accelerated Wear: to prioritise refurbishment needs and deal with sources of accelerated wear.
Set Inspection Standards: to define appearance, wear and dimensional precision requirements that ensure stable operating conditions.
Predict and Prevent Failures: to identify critical components and track deterioration patterns to stabilise and extend component life.
Improving Leader Standard Work
Establish early warning systems: to make Normal conditions visible at a glance and define actions to take when these are not met.
Develop trouble shooting algorithms to formalise countermeasures to common problems and gain insights into causal factors at trouble map hot spots.
Set work standards: to confirm compliance to best practice routines or feedback to refine current method.
Improving Planning
Set Control Points and Methods: To define effective control strategies, tolerance limits, and monitoring techniques.
Prioritise Hot Spots: to pinpoint high-risk areas or “hot spots” for immediate attention and feedback on the effectiveness of countermeasures applied.
Set Team Skill Profile: To assess current workforce capabilities, then develop targeted training and support programs.
Systems That Shape Maintenance Culture and Outlook
The scope of Lean Maintenance implementation encompasses systems that drive workforce engagement so that improved working practices are established. These are:
Policy Deployment
Eliminate Contamination: Map and resolve sources of dirt, dust and other contaminants.
Develop Shared Competencies: Build multi-disciplinary teams with the skills to troubleshoot and prevent recurring issues.
Define a 12-month improvement roadmap with quarterly checkpoints to measure progress and refine action plans.
Collaboration
Clarify Roles and Accountabilities: for sustaining basic conditions, reducing accelerated deterioration and improving reliability
Define Learning Plans: key roles to formalise best practices and standardise methods.
Reduce learning curves: Identify complex tasks and simplify to speed up competence development and compliance.
Performance Analysis
Assess Asset Criticality: to define key mechanisms, reliability issues and reduce defects.
Overall Equipment Effectiveness: to identify hidden losses and improvement potential.
Monitor Mean Time Between Intervention to track progress towards zero breakdowns and then zero defects.
Document measurable gains from enhanced reliability due to:
Standardised start-up, steady-state, and shutdown procedures.
Improved Operability and Reliability.
Control of contamination at source.
How we can help
Lean Maintenance is a proven framework to help organisations to enhance Maintenance Value, drive efficiency, reduce costs, and improve reliability—delivering long-term competitive advantage.
Are you ready to transform your maintenance strategy? Contact us to understand more about how Lean Maintenance can work for you.
DAK Consulting
Chiltern House
45 Station Road
Henley on Thames
RG9 1AT, UK
Info@dakconsulting.co.uk
www.dakacademy.com
+44 (0)1491 845504