Embedding Leadership Into Improvement
What separates high-performing organisations is the ability to align the entire organisation with a common purpose, focus cross-functional resources where they create the most value, drive with urgency and clarity, using improvement processes as a vehicle to achieve strategic goals. In short they embed leadership into the improvement process. Here is how to do that.
3 min read
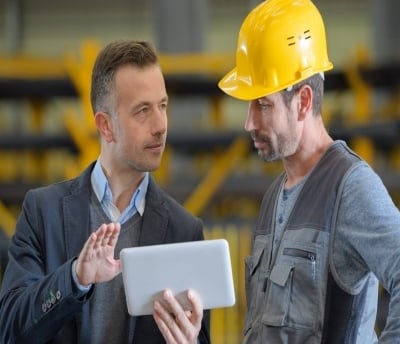
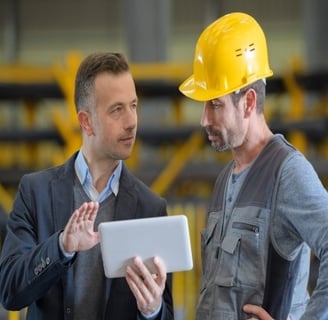
Our research into the journey towards industry-leading performance shows that progress unfolds through a series of key transitions. Each transition frees up time, strengthens capability, and enables the organisation to perform at a higher level.
This journey is not a straight line. It’s a voyage of discovery where leaders must guide the organisation to:
Stabilise performance and maintain basic operating conditions
Raise frontline capability and standardise practices to prevent breakdowns
Detect and eliminate deterioration through team-driven defect reduction
What separates high-performing organisations is the leadership ability to align cross-functional effort around each of these transitions. Specifically, these leaders:
Align the entire organisation to deliver transitions in a structured sequence
Focus cross-functional resources where they create the most value
Drive with urgency and clarity, using improvement processes as a vehicle to achieve strategic goals
Without aligned Leadership, even the best improvement tools struggle to deliver resulting in:
Competing projects fighting for limited time and resources
Localised fixes that don’t address root causes
Poor understanding of what’s really holding back performance
The outcome: high effort, low traction. Lots of activity, little measurable progress.
The Leadership Challenge
The TPM Excellence programme addresses this challenge using a series of policy deployment steps where Functional Leaders work together to:
Lead the voyage of discovery:
Use Leader Standard work to align cross functional day to day actions.
Coach direct reports to solve today’s problems while embedding processes that prevent reoccurrence.
Collaborate with colleagues to drive PDCA cycle iterations and refine work routines to establish robust, sustainable solutions.
Set targets that drive engagement and progress:
Ensure targets are realistic and resourced.
Create a clear vision, linked to business drivers and improvement goals.
Track progress and provide feedback to guide actions and reinforce progress.
Drive implementation and deepen thinking within teams:
Standardise work and simplify frontline processes to make it easy to sustain stable operation.
Break down tasks, define skills, and create learning plans to develop team wide competencies in core, intermediate and specialist levels.
Eliminate non-value activity and visual clutter to make it easy for teams to become manage their tasks and deliver excellence in all they do.
Develop communication that engages and enables:
Deliver clear, data-driven updates to provide feedback and reinforce best practices.
Coach and support teams with a compelling vision and structured development pathways to build capability and align outlooks.
The leadership role guides cross functional priorities to define an improvement agenda that:
Focuses cross-functional effort where it matters most.
Sustains gains by institutionalising new ways of working.
Links shop floor initiatives directly to business strategy.
This gives senior leaders a practical way to link local improvements with strategic business impact. Each stage of the roadmap enhances how work is done—while simultaneously freeing up leadership capacity for higher-value challenges. Without the capabilities developed at each milestone, that progression wouldn’t be possible.
Making it happen
Plan the Plan sessions create the conditions for genuine cross-functional alignment by bringing senior functional leaders together at annual and quarterly planning cycles to:
Surface interconnected challenges—not just symptoms
Agree shared priorities based on diagnostic evidence
Coordinate resource and timing to avoid duplication and friction
Build commitment to a unified improvement agenda
The deliverables from these sessions include a structured, business-led roadmap to connect operational improvement efforts directly to strategic goals—ensuring relevance, traction, and longevity.
The roadmap consists of practical improvement projects through which Leaders have the opportunity to coach direct reports as part of the day to day management routine providing:
Structured learning that builds capability across all levels
Regular progress reviews to ensure visibility and accountability
Capture and sharing lessons to embed organisational learning
Recognition and rewards to maintain motivation
Cross functional Leader Standard Work that systemises actions that underpin robust execution processes and delivery of long term business goals
These improvement projects are caried out as part of day to day operations using a quarterly cadence linked to annual business plan goals. This approach facilitates:
Delivery of annual business plans and strategy execution.
Task transfer in line with demonstrated capability development,
Systematic progress towards optimised operational capability.
It also provides a framework for recognition of team and individual achievements, reinforcing a proactive, high-performance culture.
Why It Matters
This approach enables manufacturing organisations to:
Remove hidden constraints to improvement
Align improvement priorities with long-term strategy
Break down silos and encourage cross-functional collaboration
Direct resources to where they deliver the most value
Maintain momentum through a clearly prioritised, jointly owned plan
Contact us to find out more about how we can work with your team to embed leadership development and cross-functional alignment into your improvement programme and accelerate your path to industry-leading performance.
DAK Consulting
Chiltern House
45 Station Road
Henley on Thames
RG9 1AT, UK
Info@dakconsulting.co.uk
www.dakacademy.com
+44 (0)1491 845504